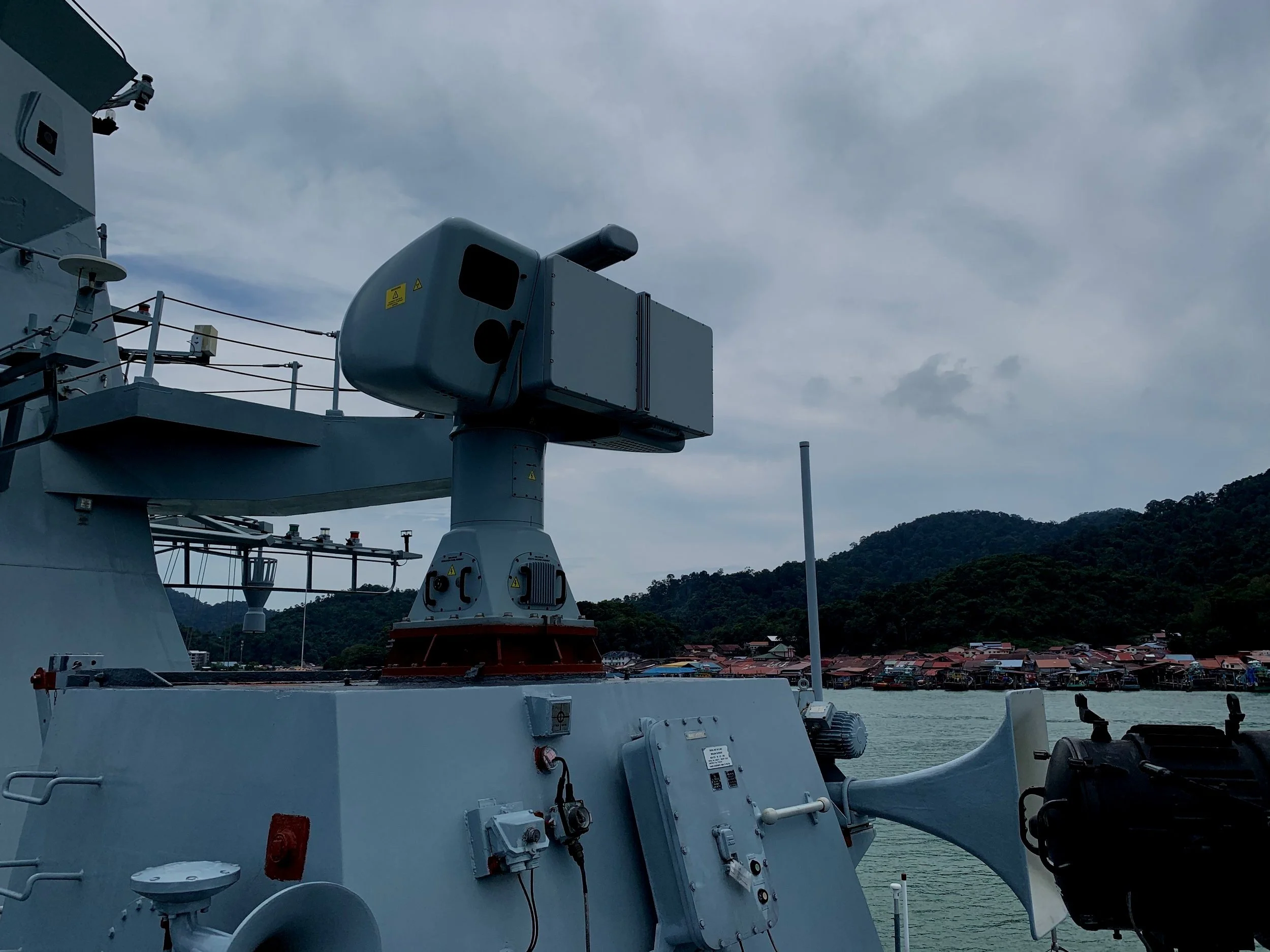
DLC Coatings
Defining Brilliance in Optical Coatings
At the intersection of advanced technology and cutting-edge design, G&H | Artemis introduces its Diamond-Like Carbon (DLC) Infrared Anti-Reflective coatings. With optimisation for 3-5 µm or 8-12 µm on Silicon or Germanium, our DLC coatings epitomise the company's prowess in confronting and mastering complex coating requirements, delivering exceptional results that transcend the boundaries of conventional optical technology.
G&H | Artemis' DLC coatings stand at the forefront of high-performance optical applications, offering superior protection and enhanced performance for a wide range of applications. From military systems to sophisticated industrial applications, these coatings can withstand challenging environments, reduce reflection and improve the longevity and effectiveness of the underlying components.
Unwavering in our commitment to quality and precision, Artemis' DLC coatings have been engineered to satisfy the stringent military environmental conditions as laid down by MIL-C-48497A, TS1888 Wiper Test, and MIL-STD-810G Method 509.5 (90 days). These military-grade standards testify to our DLC coating's durability, resistance to environmental factors, and ability to endure severe operational conditions.
G&H | Artemis' DLC coatings are crafted with meticulous attention to detail, leveraging our extensive expertise in advanced coating technologies. These coatings significantly reduce surface reflection across the designated infrared spectrum, enhancing the transmission of critical signals and ensuring clarity of information. The resultant efficiency gains and improved signal accuracy can be pivotal in demanding applications such as infrared sensing, thermal imaging or defence systems.
Designed to perform under rigorous conditions, our DLC coatings are resistant to abrasion, thermal fluctuations, and corrosive environments. This resilience ensures that the underlying optical components remain protected, maintaining their performance over extended periods of use.
Reflection < 3.5% 3-5µm @ 0° AOI
Transmission > 95% average and 90% minimum 3-5µm with an HEAR on the reverse face.
Reflection < 3% average 8-12µm @ 0° AOI
Transmission > 90% average 8-12µm with an HEAR on the reverse face.
Reflection < 3.5% 3-5µm @ 0° AOI
Transmission > 95% average and 90% minimum 3-5µm with an HEAR on the reverse face.
-
Single layer of Diamond like Carbon
Optimised for 3-5 µm or 8-12µm on Silicon or Germanium
-
Silicon
Germanium
Zinc Sulphide
Zinc Selenide
Calcium Fluoride
Barium Fluoride
Magnesium Fluoride
Chalcogenides
Nickel-plated Aluminium
-
MIL-C-48497A
TS1888 Wiper Test
MIL-STD-810G Method 509.5 (90 days)
-
Thermal imaging: Infrared anti-reflective coatings are widely used in thermal imaging systems, where they help to enhance the performance of lenses and windows, improving image quality and detection capabilities.
Military and defense: In military applications, such as night-vision devices and surveillance systems, DLC infrared anti-reflective coatings provide enhanced optical performance and durability, enabling reliable operation in harsh environments.
Remote sensing: In remote sensing systems, these coatings can improve the transmission of infrared light, resulting in higher-resolution data and more accurate measurements.
Laser systems: In laser-based applications, DLC infrared anti-reflective coatings help to reduce reflection losses and optimize the transmission of laser light, improving the overall efficiency and performance of the system.
Medical devices: Infrared anti-reflective coatings can enhance the performance of medical devices that utilize infrared light, such as diagnostic equipment and surgical tools, enabling more accurate diagnoses and more precise procedures.